Die cutting involves the use of a specialized die—crafted with the exact dimensions of the desired component—to cleanly cut, shape, or engrave materials. This process is vital in industries ranging from automotive and aerospace to electronics, medical devices, and packaging.
Advances in technology have taken die cutting from manual hand-press systems to highly automated machines capable of producing intricate designs at incredible speeds. However, the principles remain the same: precision, repeatability, and quality control.
What sets die cutting apart from other fabrication methods is its ability to handle high volumes while maintaining exact tolerances. With the right die and process, manufacturers can ensure components integrate seamlessly into broader assemblies.
Types of Die Cutting Techniques
Die cutting is not a one-size-fits-all process. The choice of technique depends on the material, complexity of the design, and volume of production. Below are three commonly used techniques in the industry along with their strengths and applications.
Rotary Die Cutting
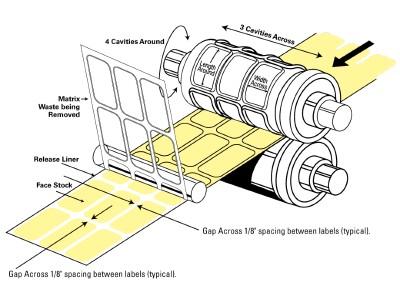
Rotary die cutting is the workhorse of high-volume production. This technique uses cylindrical dies mounted on rotating rollers to cut, perforate, or score materials as they move through the machine. It’s ideal for thin, flexible materials like foams, films, and tapes, where precision and speed are paramount.
Experienced die cutters often use rotary die cutting for continuous roll-to-roll production. For example, when producing foam seals for the automotive industry, the rotary die cutting machine ensures a seamless process, from feeding raw materials to outputting finished components. One of its unique advantages is its ability to handle multiple processes in a single pass—cutting, laminating, and slitting—saving time and reducing costs.
Flat-Bed Die Cutting
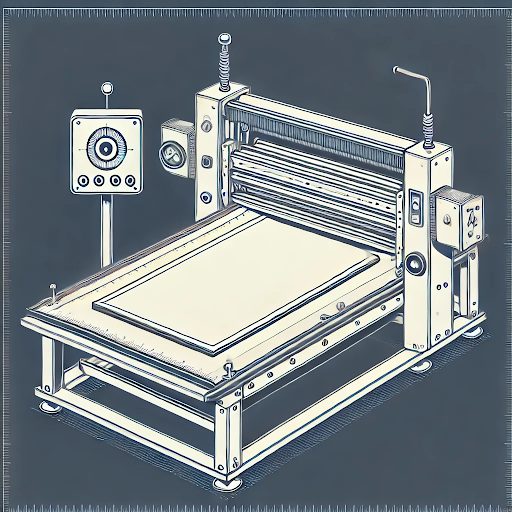
Flat-bed die cutting is known for its ability to handle thicker, more rigid materials with accuracy. This method involves a flat die that presses down on the material to create the desired shape. Unlike rotary die cutting, which is continuous, flat-bed die cutting operates in a start-stop manner, making it ideal for low to medium-volume projects that demand tight tolerances.
For example, die cutters will use flat-bed processes when working with thicker rubber or plastic sheets that are used in construction or energy applications. The press provides consistent pressure across the entire surface, ensuring clean edges and minimal material distortion.
Steel Rule Die Cutting
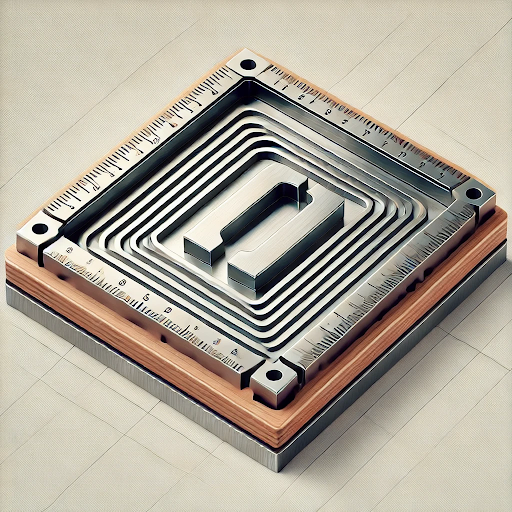
Steel rule die cutting is a versatile and cost-effective technique often used for less complex designs or prototypes. It involves a steel blade embedded in a base—usually wood or metal—that’s shaped to match the component’s design. The material is then pressed onto the die to cut the shape.
We frequently recommend steel rule die cutting for projects with straightforward geometries, such as cardboard packaging inserts or gaskets for electronics. The beauty of this method lies in its adaptability and affordability, particularly for small-scale production runs where precision is still a priority.
Materials Used in Die Cutting
Selecting the right material for a die cutting project is just as crucial as choosing the right cutting technique. The type of material dictates everything from the cutting method to the achievable tolerances and final application.
Rotary die cutting is best suited for thin, flexible materials, particularly those under 0.015 inches thick, as the rolling action of the die ensures precision cuts at high speeds. Flatbed die cutting, on the other hand, can handle thicker and more rigid materials, as its press-style action allows for even force distribution.
Below are some of the most commonly used materials in die cutting, the preferred cutting method, and common industrial applications:
Common Die Cutting Materials & Applications
Material | Preferred Cutting Method | Common Applications |
---|---|---|
Plastics (PET, PVC, Polycarbonate) | Flat-bed for thicker sheets Rotary for films under 0.015″ |
Medical device components, electronic insulation, ID cards, packaging films |
Foams (Open-cell & Closed-cell) | Rotary for thin gaskets & seals Flat-bed for thicker padding |
Automotive gaskets, medical padding, industrial insulation, soundproofing |
Rubber (Neoprene, EPDM, Silicone) | Flat-bed for thicker sheets Rotary for thin seals |
Gaskets, vibration dampeners, sealing solutions for aerospace & HVAC |
Paper & Cardstock | Rotary for high-speed production Flat-bed for specialty cuts |
Packaging inserts, custom labels, printed marketing materials |
Tapes & Adhesives (3M, Acrylic Foam, Double-Sided Tapes) | Rotary for roll-to-roll conversion | Electronics bonding, automotive attachment, medical adhesives |
Fibers & Non-Woven Materials | Rotary for flexible applications Flat-bed for rigid sheets |
Filtration systems, protective face masks, automotive acoustic insulation |
Metal Foils (Aluminum, Copper, Stainless Steel under 0.015″) | Rotary for ultra-thin foils Flat-bed for slightly thicker sheets |
EMI shielding, conductive gaskets, aerospace heat shielding |
Textiles (Kevlar, Nylon, Polyester Fabric) | Flat-bed for thick or multi-layer fabrics Rotary for thin layers |
Safety gear, industrial filters, insulation linings |
Material Selection Considerations
Beyond just thickness and flexibility, other factors that influence material choice in die cutting include:
- Tolerances & Precision: Certain materials, like rubber and foam, have higher compression rates and may require tighter process control to maintain dimensional accuracy.
- Adhesive Backings: Many materials, particularly tapes and films, come with adhesives that must be accounted for when choosing a cutting method.
- Durability Requirements: Applications such as aerospace and medical components demand materials with high resilience and precision.
Die Cutting Process Setup & Execution
Die Cutting Compared to Other Cutting Solutions
There are numerous cutting options available to make a variety of components, including the latest options like waterjet and plasma cutting. However, when it comes to material versatility, efficiency and precision, die cutting offers numerous benefits. Below are scenarios where getting die-cut components makes engineering and budgetary sense.
Cutting Technique | When & Why Die Cutting is Preferred | Non-Obvious Application Where Die Cutting Makes Sense |
---|---|---|
Die Cutting | Best for high-volume production with repeatable precision. Cost-effective for simple and complex shapes in soft or flexible materials. | Medical-grade adhesive bandages, which require precise cuts in soft, flexible material for large-scale production. |
Laser Cutting | Die cutting is preferred when speed and cost are priorities, as laser cutting can be slow and expensive for high-volume runs. | Gasket manufacturing in the automotive industry, where die cutting outperforms laser cutting for speed and material efficiency. |
Waterjet Cutting | Die cutting is more efficient for thin, non-metallic materials, as waterjet cutting is better suited for thick and heat-sensitive materials. | Mass production of disposable filtration media, where die cutting ensures consistent quality and high output. |
CNC Routing | For thin materials requiring large batch production, die cutting is more efficient than CNC routing, which is better for complex 3D parts. | Production of electronic insulation films, where die cutting provides fast, high-precision cuts without excessive tool wear. |
Plasma Cutting | Die cutting is ideal for non-metallic materials, whereas plasma cutting excels at thick metals requiring high heat processing. | Manufacturing of foam cushioning inserts for packaging, where die cutting enables rapid cutting of various foam densities. |
Wrapping Up
Die cutting advances in recent decades have increased the speeds at which rotary presses can run and tightened up tolerances for a wide variety of materials. However, the biggest differentiator in the quality and precision of components from a die cutting supplier comes from their experience with similar materials and deep understanding of their machine’s operation.
For a variety of flexible and thin materials, working with an experienced die cutter ensures that parts can meet tolerances as tight as ±0.005 inches, ensuring fitment in the most demanding applications like electronics, medical devices and others. To learn more about how die-cut components can accelerate your production timeline, contact the team with 75 years of experience at Colvin-Friedman. You can either fill out the short form or contact Vice President Josh Rodman directly about your project needs at (707) 769-4488.